In prepping for first engine start, I first had to get fuel flow testing done. I started out by putting 5 gallons of fuel in each tank sloshing it around a bit and draining it back out by pulling the sump drain. This flushed the tank of any construction debris, which there were only a couple of small metal chips found.
For safety sake, I had my extinguisher out and ready at all times, and I also bought a metal funnel which I bolted on a wire to with an alligator clip on the other end to ground to the airplane skin. On this same bolt, on the inside of the funnel, I attached a long piece of safety wire which went down through the funnel and was extra long to sit inside the container catching the fuel so it was touching the liquid as well. I also grounded the airplane with a separate wire to the metal hangar building, although this is less important as it is to have the funnel and container/liquid at the same potential as the airplane so no static can build up.
I then put 5 gallons back into each tank and ran each fuel pump, checking for leaks as fuel was circulating through the whole system. I adjusted my fuel pressure regulator to 46psi statically with the engine not running.
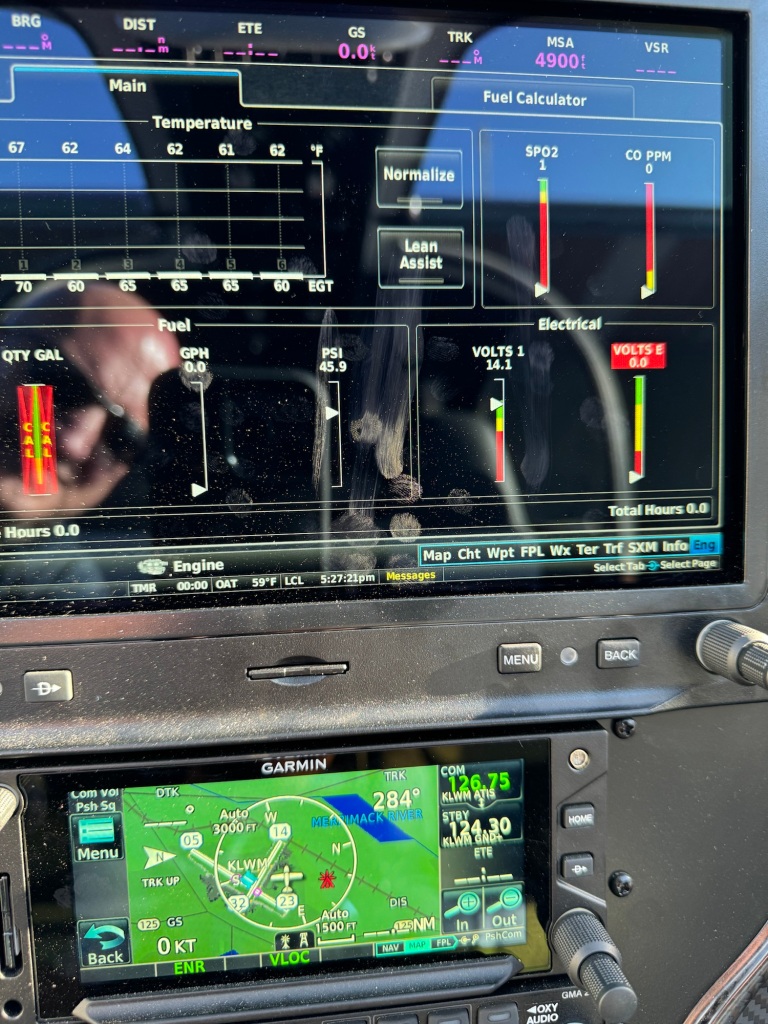
Then it was on to the fuel flow tests. First I pumped all the gas out by unhooking the return hose and running the pump until it cavitated. Then I collected what was left in the tank via the drain sump. A very small amount was left in each tank.
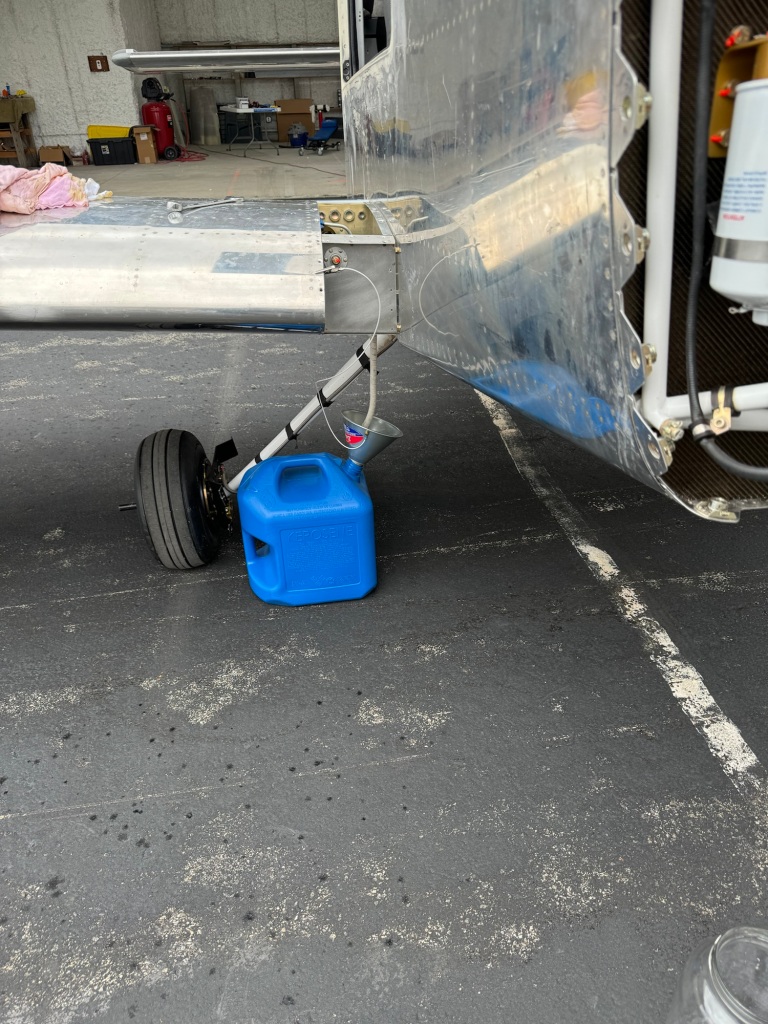
Then fuel was added back to the tank and again the return hose was used to fill a 1 Gallon glass container while the pump ran for 1 minute in a flight level attitude. I almost filled the 1 gallon in a minute.

Weighing it, I got a little over 4 lbs. Avgas is around 6 lbs/gal and the temps were in the high 40’s low 50’s, so the density of the fuel should be close to the 6 lbs/gal. Doing the math to convert weight per minute to gallon per hour nets me > 48 Gallons per hour delivery. I did each tank twice once from each fuel pump to make sure each pump can deliver at least 150% of what the engine needs at full power.
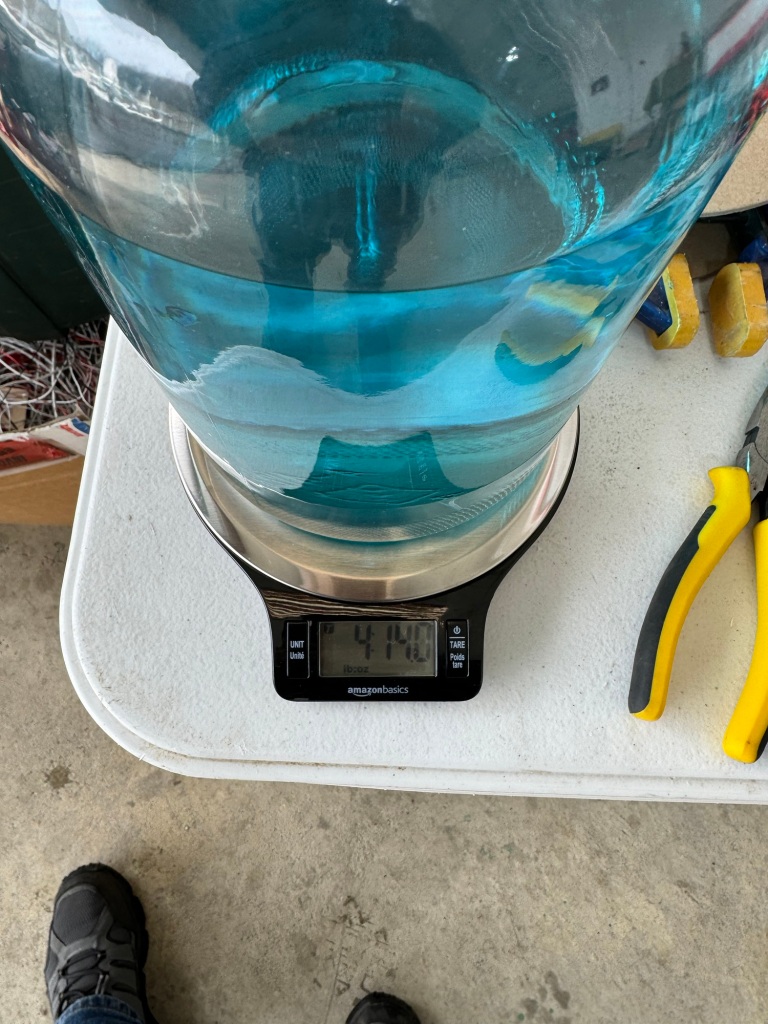
I then lifted the nose up as much as I could before the tail hit to simulate a nose up attitude. The 4 tests were repeated and netted close to the same results.

Then it was on to putting oil into the sump and filling the oil cooler.

Once things were oiled up, I left the top plugs out, disconnected the bottom plug wires, shut off the fuel and ignition, and cranked the engine to pre-oil the engine. This ends when you start to build up oil pressure as shown below.
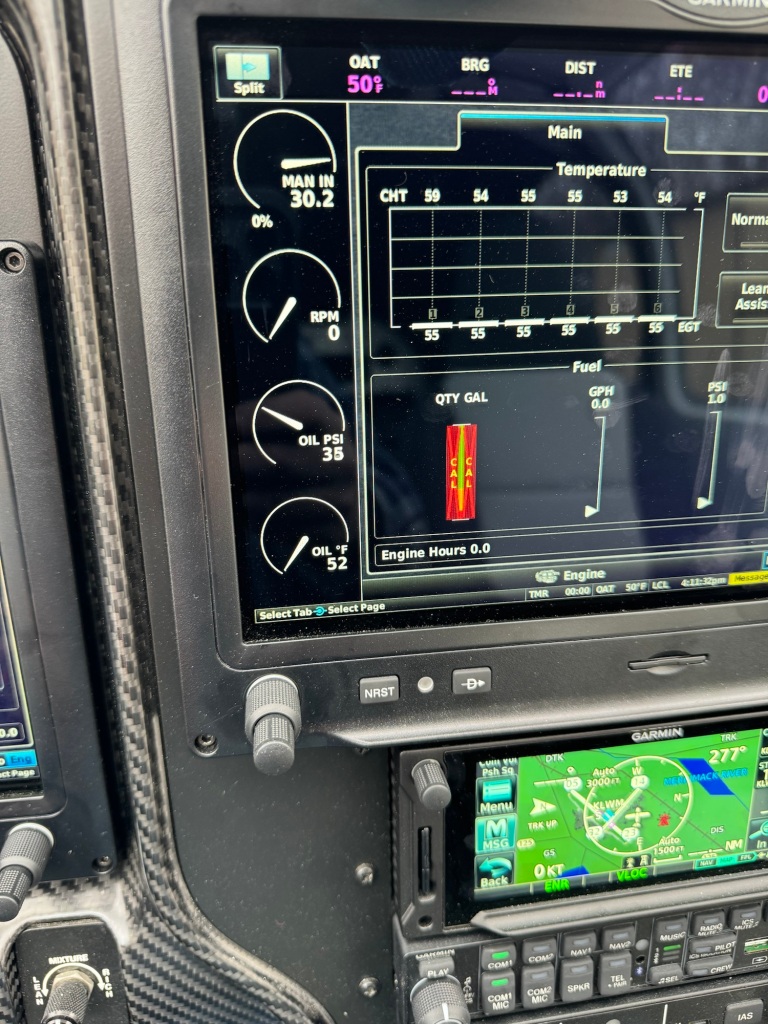
After spending some time double checking that the SDS system was seeing the flywheel magnets, programming all the gauges for green/yellow/red range markings, etc… I was confident that I was ready to try to start the engine for the first time. I used my truck to strap the plane to just in case something happened with the brakes. Fire extinguisher at the ready.. and I asked a fellow EAA member to come by to keep an eye on the engine while I ran it for about 3 minutes. I ran around 1000 RPM for a minute and a half or so, and then went to 1700 RPM and cycled the prop a couple of times successfully.


A quick snap of the engine gauges while it was running. Everything seems normal.
I let the engine cool down and then ran it one more time before putting it away for the day.
I’ve since been able to do some short taxi tests to set the brakes and also calibrate the magnetometer. Now it’s time to do W&B and get ready for the inspection.
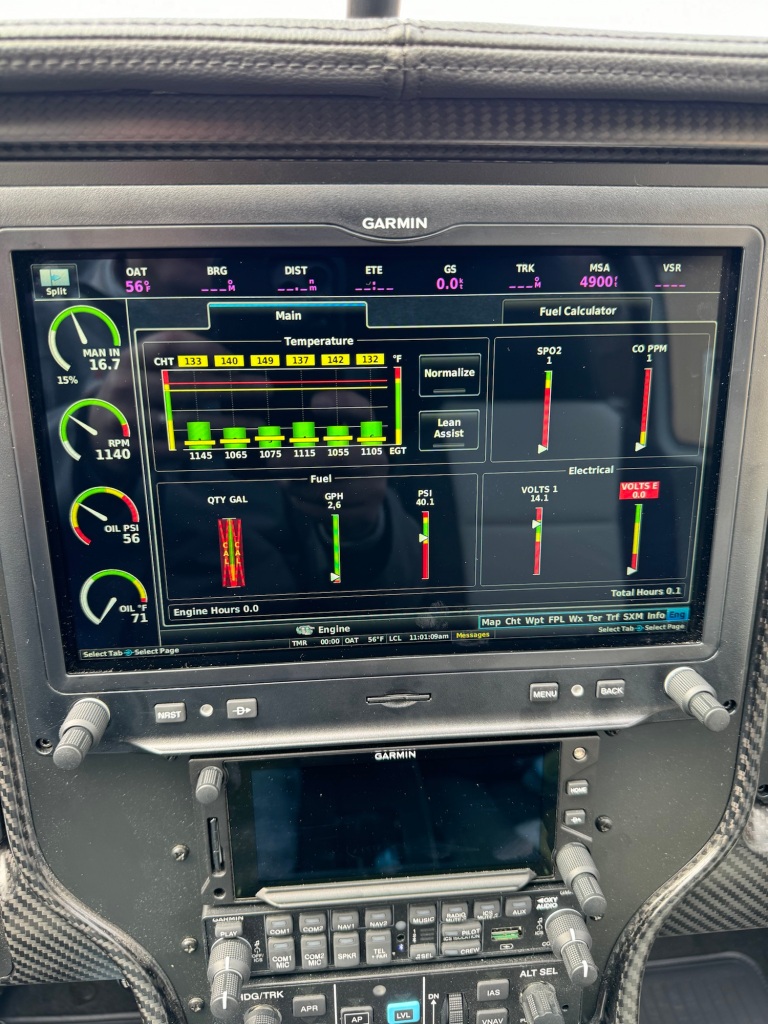